
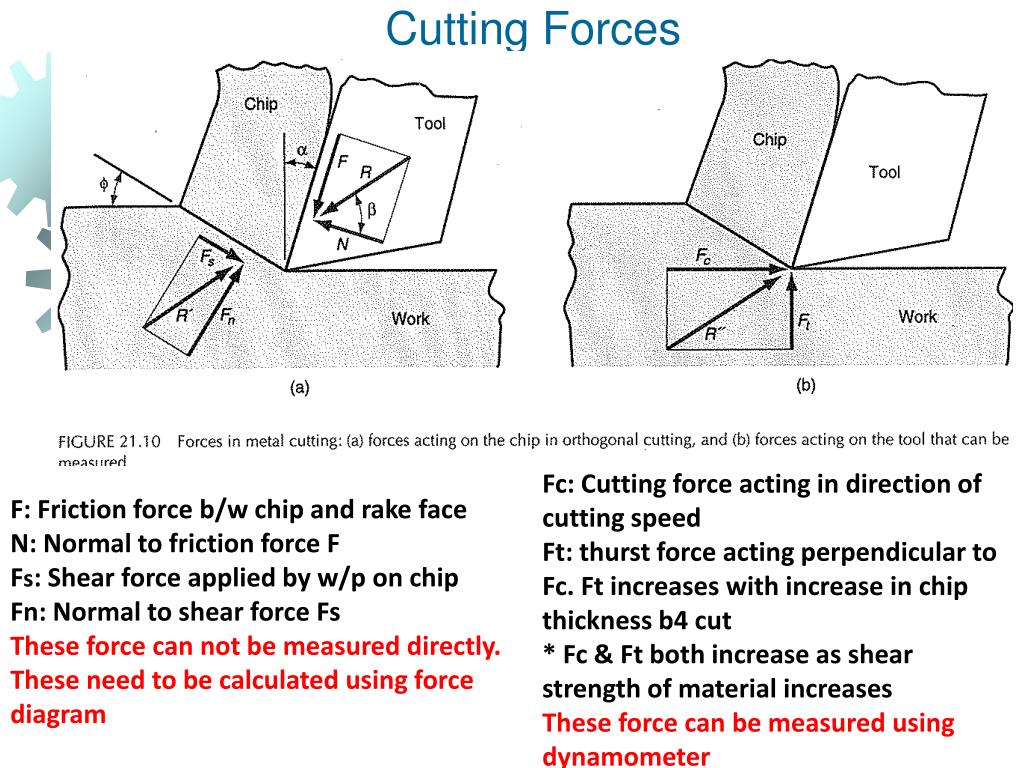

These tests confirm that the radial force presents an increasing behaviour until. Finally, the values for temperature, resultant forces and chip compression ratio as attained by experiment are compared with those calculated with the FEM cutting model. cut of the hard steels causes the formation of serrated chips called. In this study, from the basic knowledge of orthogonal cutting until the. The course of the obtained results is explained using the correlation between the capacity produced by the heat source and its retention period in the temperature range under consideration. In addition, the resultant forces and the chip compression ratio were determined as further characteristic machining variables. To verify the model, the temperature was measured in the secondary shear zone and at the exterior surface of the chip, which was analytically estimated as well and compared with the experimental values. Explain the main features of an orthogonal cutting operation. This paper describes the procedure for creating and verifying a thermomechanical FEM model of orthogonal cutting processes as well as the results obtained with this model. Why is it not always advisable to increase the cutting speed in order to increase the.

Therefore it is important to understand how the change of cutting speed affects on the surface integrity in inconel718 alloy machining6. The model is based on phenomenological aspects: energy approach combined with the friction and the plastic deformation of the material. Their results show that severe tool wear occurs. The heat distribution of the cutting tool, tool-chip interface and workpiece provided effective and useful data for the optimization of selected cutting parameters during orthogonal machining. addressed the machinability of PM high-speed steels during longitudinal and orthogonal hard turning. rate and depth of cut, the tool temperature increased the cutting speed was found to be the most effective parameter in assessing the temperature rise. The research indicates that the chip morphology transforms from serrated to fragmented at the cutting speed of 7000 m/min due to embrittlement of the workpiece material under ultra-high. metallic particle emission during orthogonal cutting. In addition, the microvibrations during cutting and the low thermal conductivities of sintered PM components due to their internal porosities will facilitate the further tool wear. Heisel, Uwe Storchak, Michael Krivoruchko, Dmitrii Cutting pressure and temperature decrease with increase in cutting speed in high-speed machining. Meanwhile, experiments of high-speed orthogonal cutting are performed to verify the simulation results with cutting speeds ranging from 50 m/min to 7000 m/min. Thermal effects in orthogonal cutting Thermal effects in orthogonal cutting
